Wir haben eine neue Telefonnummer: +49 39203 281 100
News
Entdecken Sie unsere neueste Innovation - LiquiScope!
LiquiScope – Ihre Lösung, um Fehlbefüllungen zu vermeiden und Prozesse sicherer zu gestalten
Permanente Überwachung im Beizbad
Unser Messsystem LiquiSonic® ermittelt Dichte und Konzentration von Prozessflüssigkeiten auf Basis der Schallgeschwindigkeit. Die Messungen finden…
SensoTech & BioEconomy
🌱 Sensorik trifft Bioökonomie – ein spannender Austausch in Leuna! 🔬⚡
Am 6. März 2025 waren wir beim BusinessTreff Sensorik des Bioeconomy Cluster im…
Bevorstehende Events
25. - 26. Juni 2025
H2 Hydrogen Technology Expo 2025
Houston, TX, USA
10. September 2025
MEORGA
Ludwigshafen, Germany
07. Oktober 2025
Parts2Clean
Stuttgart, Germany
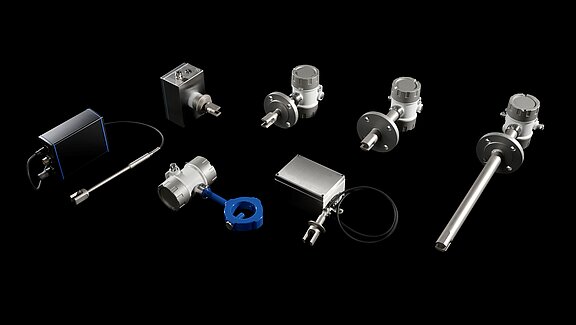
SensoTech ist der Spezialist für die Analyse und Optimierung verfahrenstechnischer Prozesse in Flüssigkeiten.
Seit der Gründung 1990 haben wir uns zum führenden Unternehmen für Messgeräte zur Inline-Bestimmung von Konzentrationen in Flüssigkeiten entwickelt.
Unsere Analysesysteme bestimmen den Trend – weltweit.
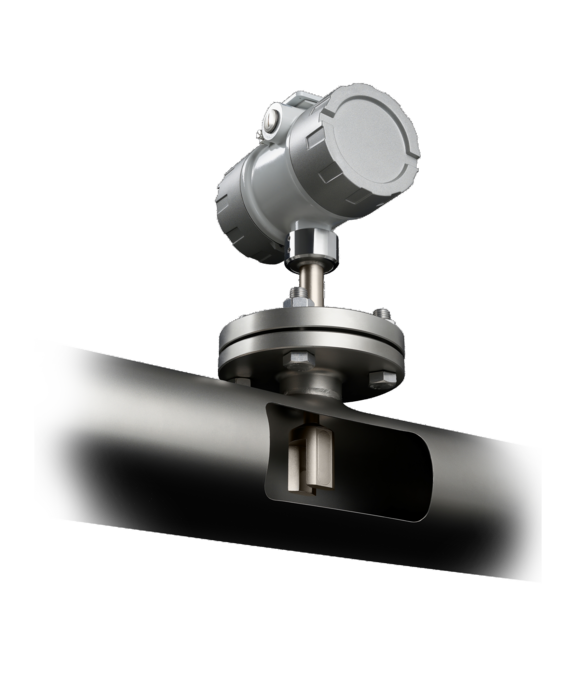
LiquiSonic® misst die Dichte bzw. die Konzentration einer Flüssigkeit mit Hilfe der Schallgeschwindigkeit. Das Messverfahren ist dabei unabhängig von Leitfähigkeit, Farbe, Brechungsindex oder Transparenz der Flüssigkeit.
Wir bieten für unsere Kunden verschiedene Varianten an, die für die unterschiedlichen Einsatzgebiete angepasst sind.
Ihr Prozess, unsere Lösung - einfach, schnell, genau.
SensoTech ist der Spezialist für die Herstellung von Messgeräten zur Inline-Bestimmung der Konzentration und Dichte in Flüssigkeiten. Diese verwenden die Schallgeschwindigkeit um die Flüssigkeiten zu analysieren.
Unsere Messsysteme werden in verschiedenen Prozessen in Branchen wie der Chemieindustrie, Pharmaindustrie, Lebensmittelindustrie und vielen weiteren verwendet. Kunden aus aller Welt vertrauen auf die Expertise und Qualität unserer LiquiSonic® Messgeräte, um ihre Prozesse zu optimieren und selbst unter den schwierigsten Bedingungen hochgenaue Messergebnisse zu liefern.
Nach Installation und Inbetriebnahme stehen wir Ihnen als kompetenter Partner bei allen Fragen zu Ihrem System zur Seite. Erstklassiger Service bildet für uns neben der Entwicklung hochmoderner Messgeräte eine wichtige Stütze, um unserem Qualitätsanspruch gerecht zu werden.
Neben erstklassigen Produkten und umfangreichem Service bieten wir unseren Kunden eine Reihe von Events und Webinaren. Ein etabliertes Netzwerk und unsere zahlreichen internationalen Vertretungen in allen wichtigen geografischen Märkten der Welt, in welchem unser Expertenwissen erweitert wird, ist die Basis für innovative Lösungen, welche am Markt Maßstäbe setzen.
Wir haben die Lösung für Ihr Problem!
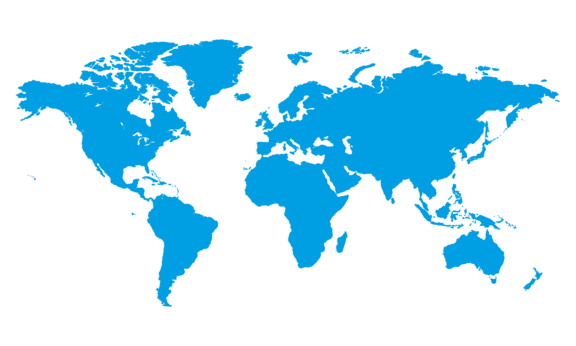
Hauptsitz
SensoTech GmbH
Steinfeldstr. 1
39179 Magdeburg-Barleben
Deutschland
T +49 39203 281 100
F +49 39203 281 109
info@~@sensotech.com
Niederlassungen
SensoTech Inc.
69 Montgomery Street, Unit 13218
Jersey City, NJ 07303
T +1 973 832 4575
sales‑usa@~@sensotech.com
SensoTech (Shanghai) Co., Ltd.
Room 609, Bldg.1, No.778, Jinji Road. Pilot Free Trade Zone,
201206 Shanghai
China
T +86 21 6485 5861
F +86 21 6495 3880
www.sensotechchina.com
sales-china@~@sensotech.com